Workflow
Quote Request
You will need to provide all specifications for your print job to the sales staff/CSR, being sure to include shipping and delivery information as well. Our estimating or sales staff may suggest alternate ideas, providing cost savings, and better products.
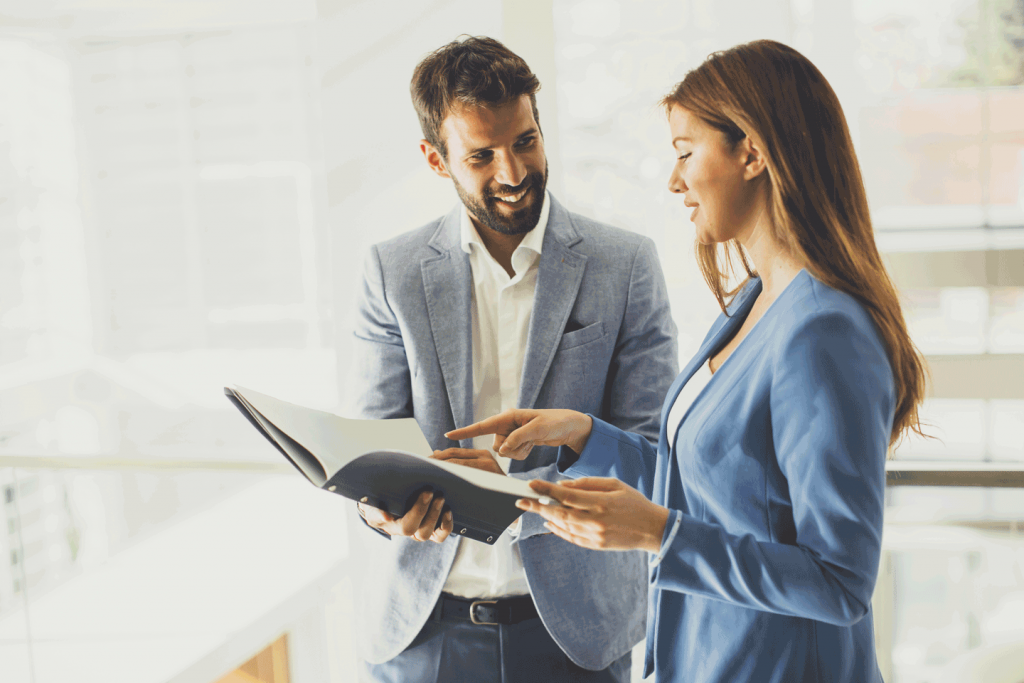
Quote Approval
All quotes must be approved before production beginning. Fax, scan signed estimate, or send us an email stating that estimate # ____ is approved for ____ quantity.
This would be an ideal time to request your desired in-hand date and provide additional information.
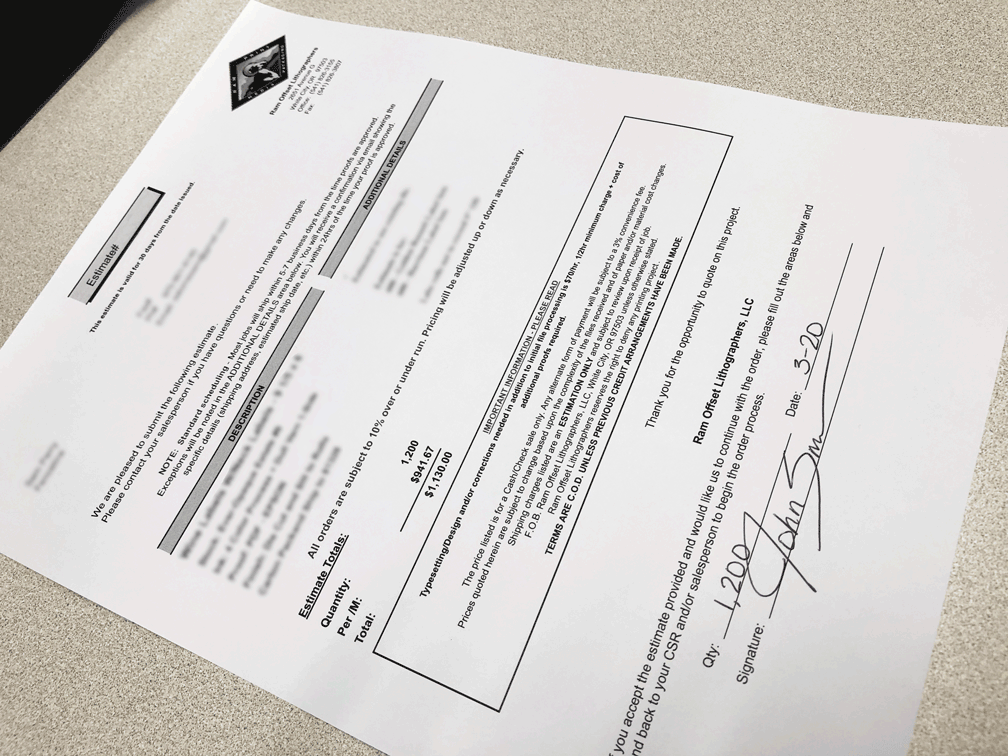
Submit Artwork / Design
If your artwork is press-ready, submit the files to us via our upload link.
If your project needs to be designed by our graphics department, communicate with sales or customer service to get the design started.
- Depending on the size of your project, our design staff may work directly with you to obtain all of the necessary elements and show you digital proofs as the piece is designed. Once the design proofs are approved, the following steps will commence.
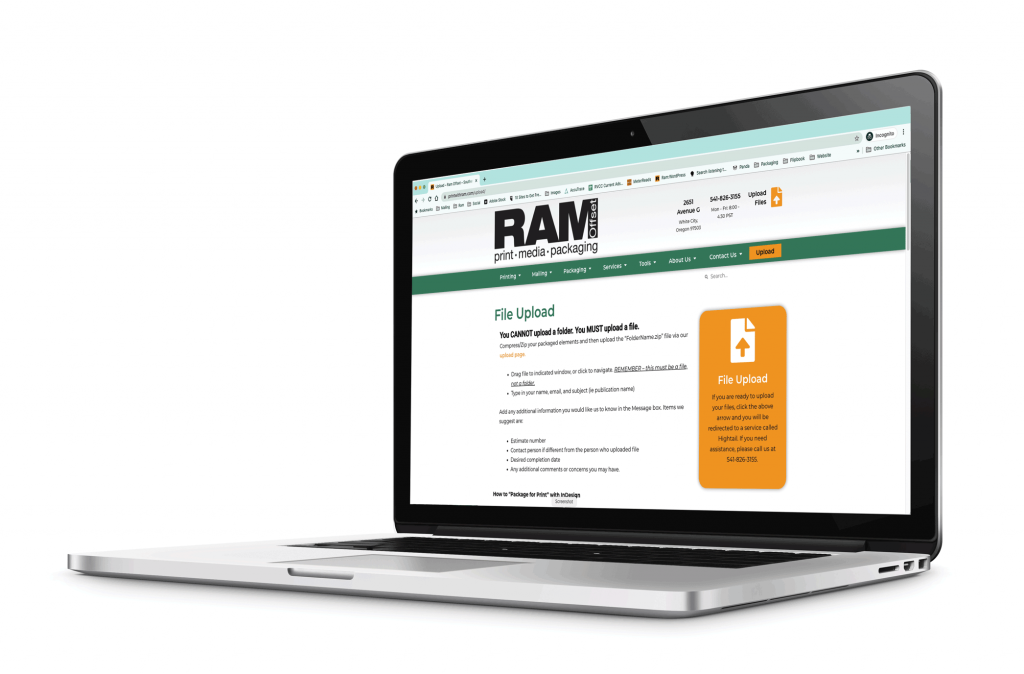
Flightcheck/Preflight
All files are reviewed for low resolution, bleed issues, live area, black builds, etc. A preflight report will be provided to you either independently or along with the digital proof of your project.
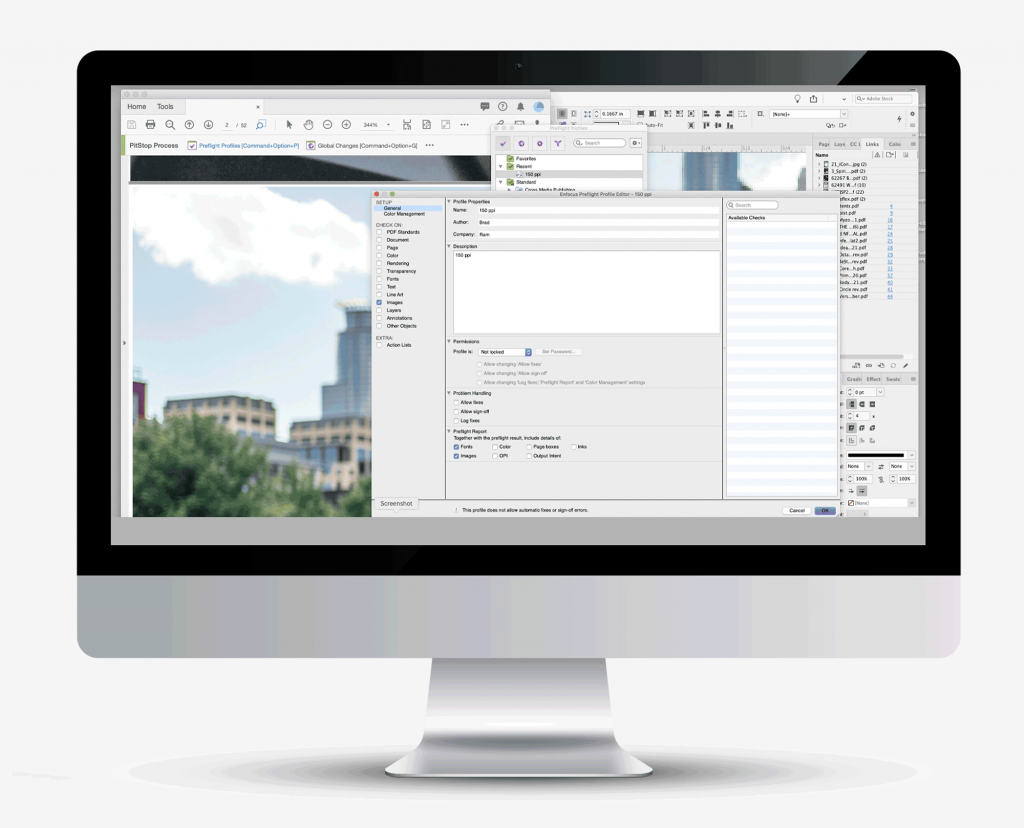
RIP and Proof
Raster Image Process, or RIPping, of your files, is necessary to prepare them for the press. This is when the Interpretation, Rendering, and Screening occurs as well as pagination.
- Hard Copy Color Proof: High quality, color-calibrated Epson proofs are generated for you to review color accuracy on the press. (These epsons need to be returned to Ram so the press operator can match them when printing.)
- Imposition Proof: A to-size print generated on a thinner stock, allowing us to fold and assemble the pages in the sequence the bindery will assemble the printed pieces.
- Soft Proof: A paginated pdf of the ripped pages sent to you electronically for you to review on your computer.
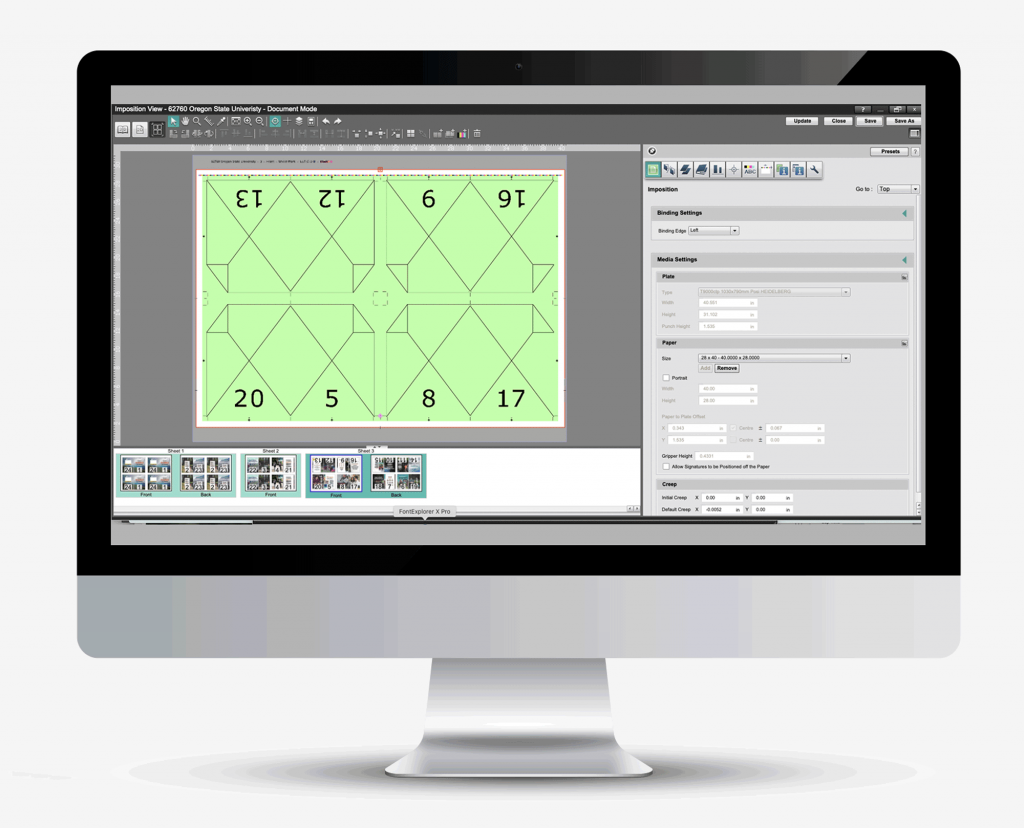
Revisions or Proof Approval
After you have reviewed your hard copy or digital proofs, you will need to inform Ram in writing of any revisions or if your project is ready for printing.
If you provide new pages or files, a detailed list of what has changed is required. The prepress work will take place and you will be sent another proof for review.
Once an approval of the proof has been received and the hard copy proofs have been returned to Ram, your project will be scheduled on the press.
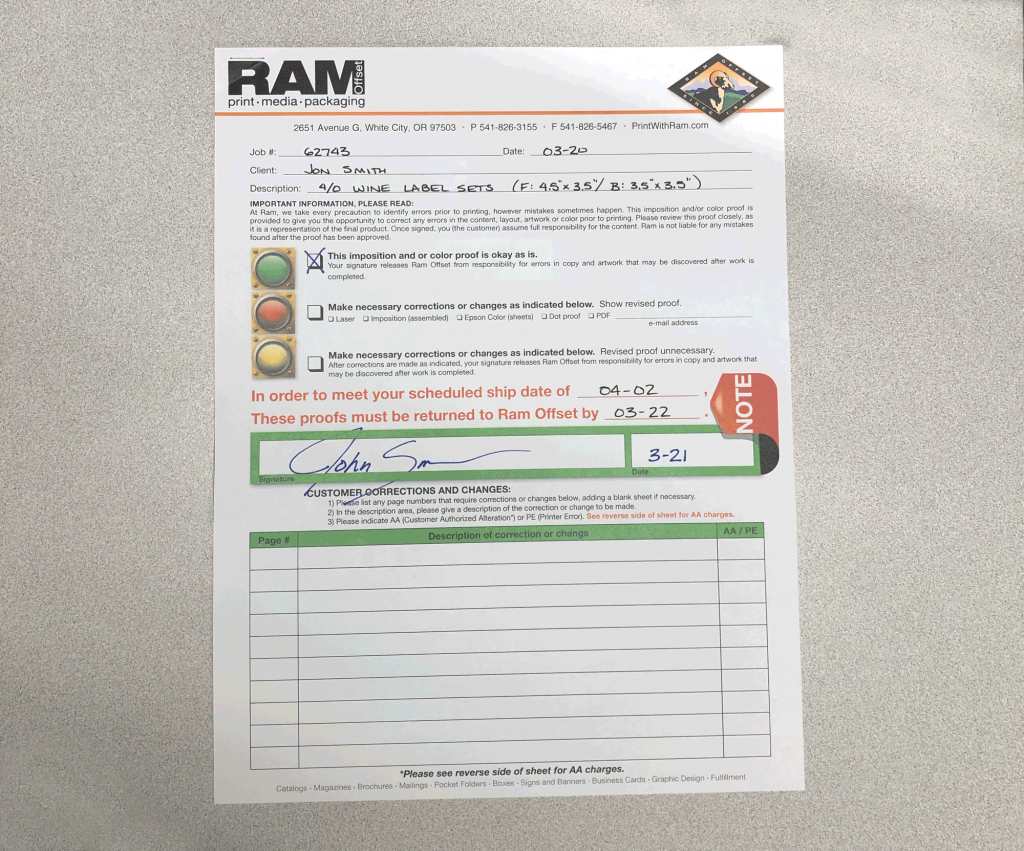
Plate
A printing plate is a thin piece of aluminum that has a coating we expose in our plate imagesetter. A plate is made for each color: cyan, magenta, yellow, and key (black.) Once exposed and processed, this printing plate is placed around a cylinder on our offset presses.
The artwork imaged on these plates indicates where the ink should be transferred to the blanket during the process of offset printing.
The plate process is not required with our digital presses.
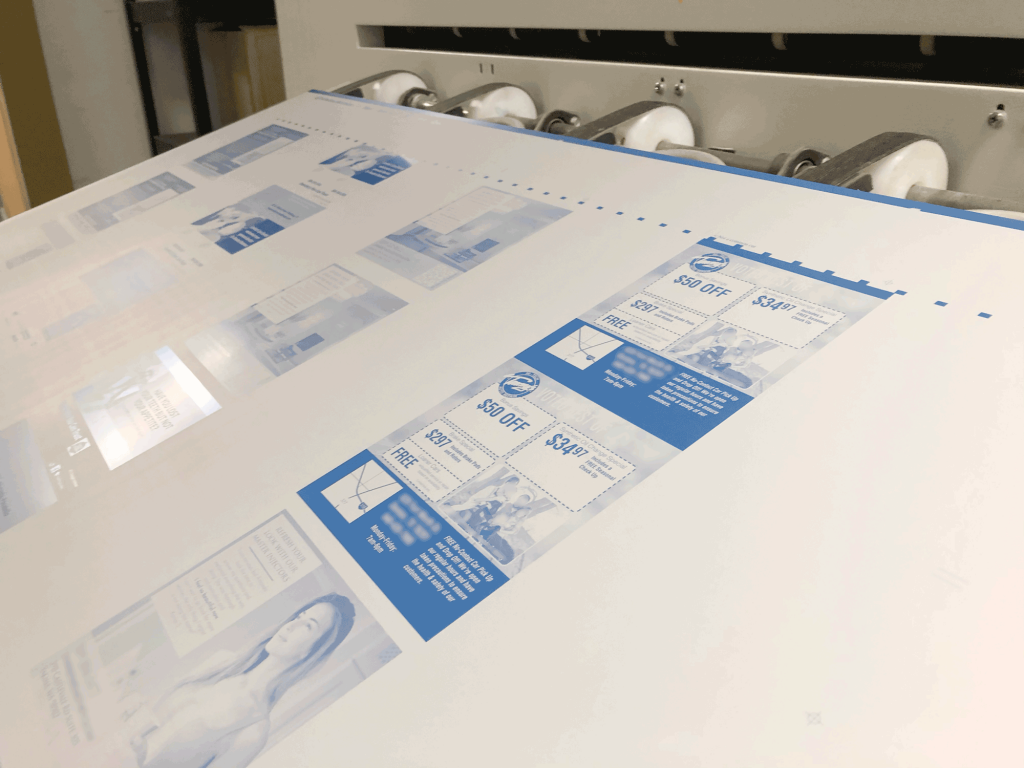
Many variables dictate how long your job will take to produce once it is on the press. Quantity, stock, page count, and dimensions are a few elements that will determine if your job will take hours or days on our printing presses.
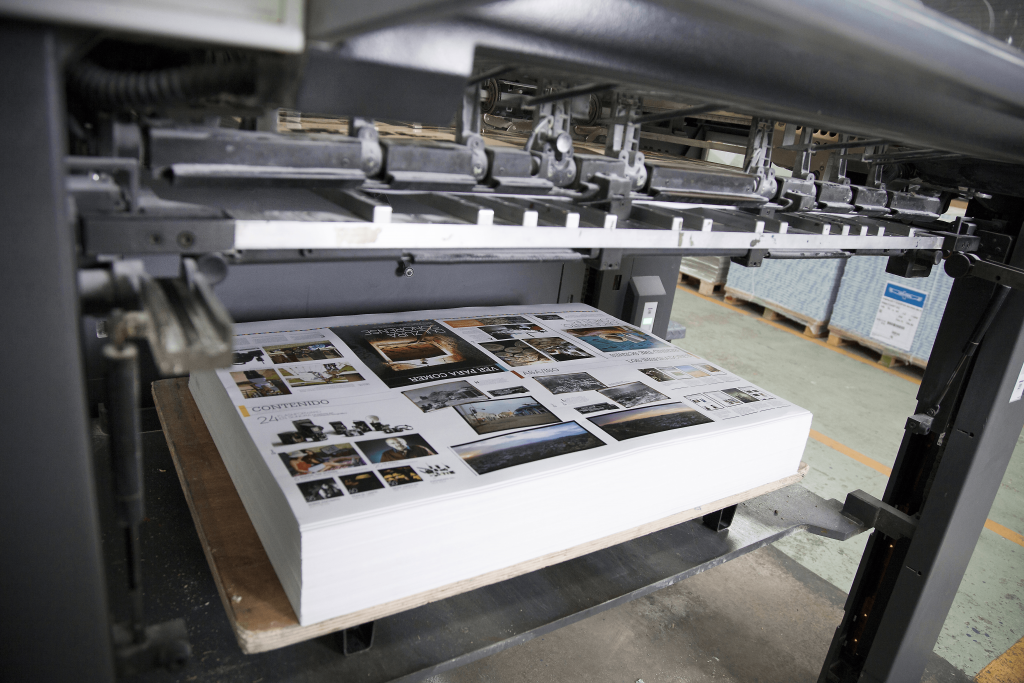
Bindery
As with printing, many variables dictate how long your job will take in our bindery department. Once the pieces are all printed, the assembly and finishing process can begin.
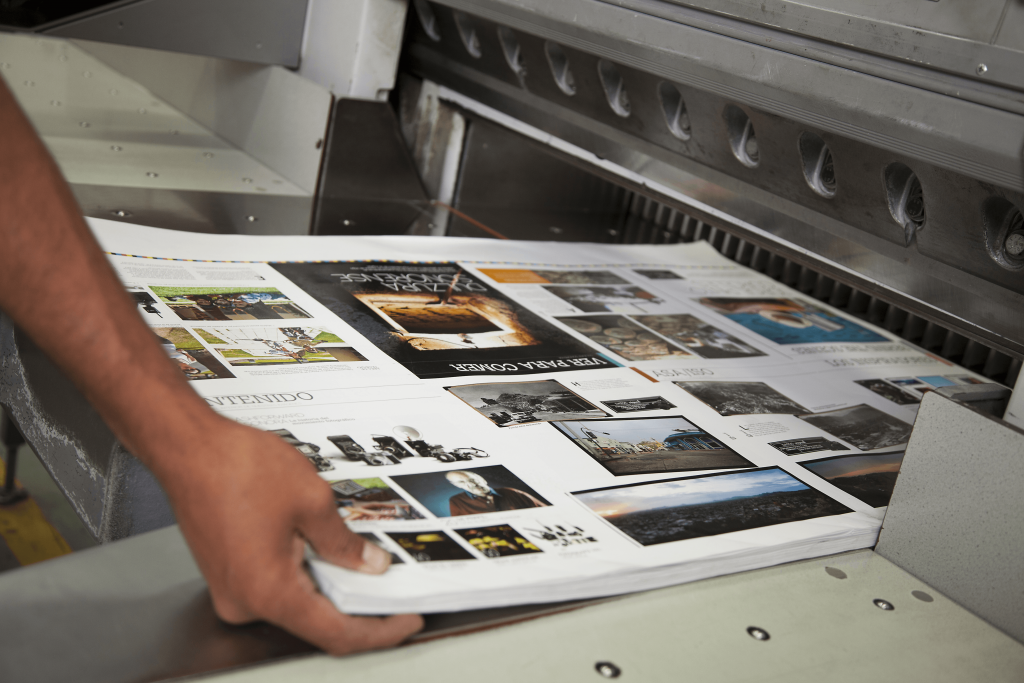
Mailing
If we are mailing your piece for you, ideally the mail list has been processed and prepared simultaneously as the job was being printed and finished in the bindery. This allows a seamless workflow for your piece to enter the mail department as soon as it is completed in the bindery.
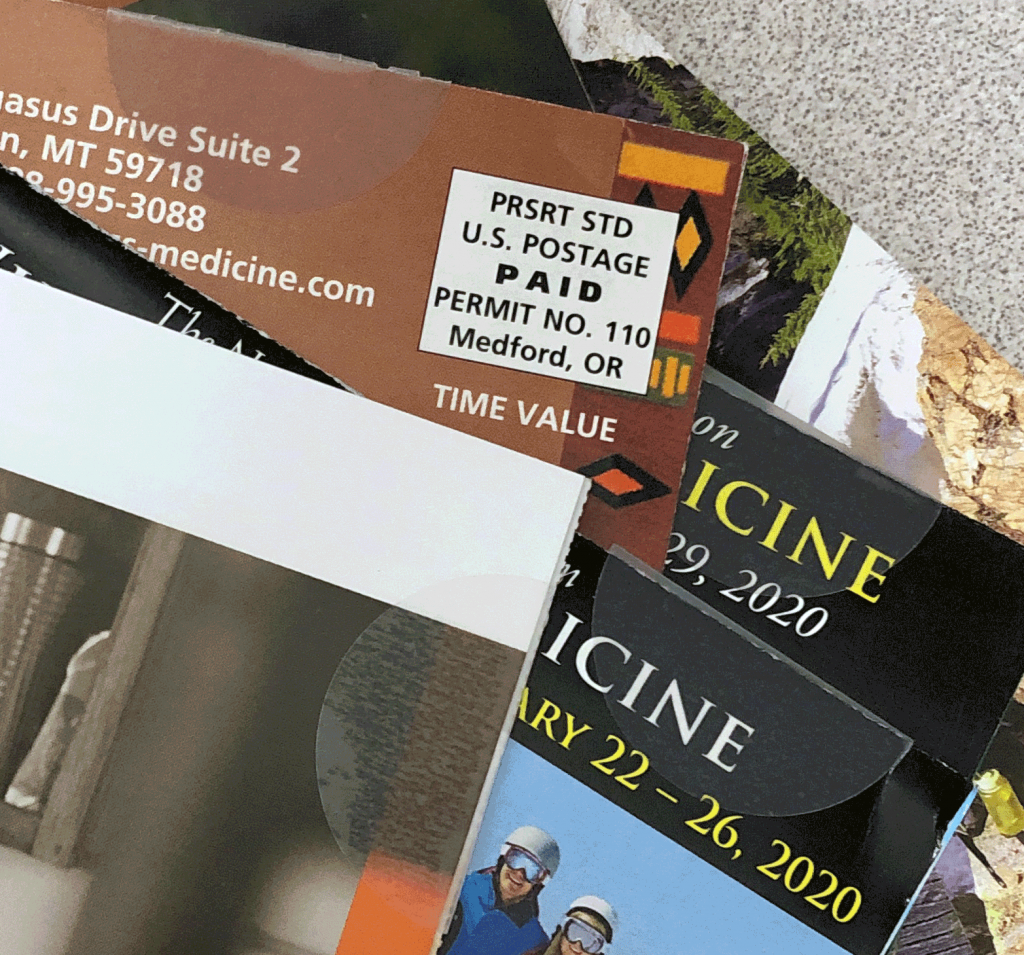
Shipping
During estimation and job entry, all of the shipping details were provided to the sales/CSR. This allows us to have packaging and shipping information prepared when your printed piece reaches the shipping area, resulting in efficient and cost-effective delivery.
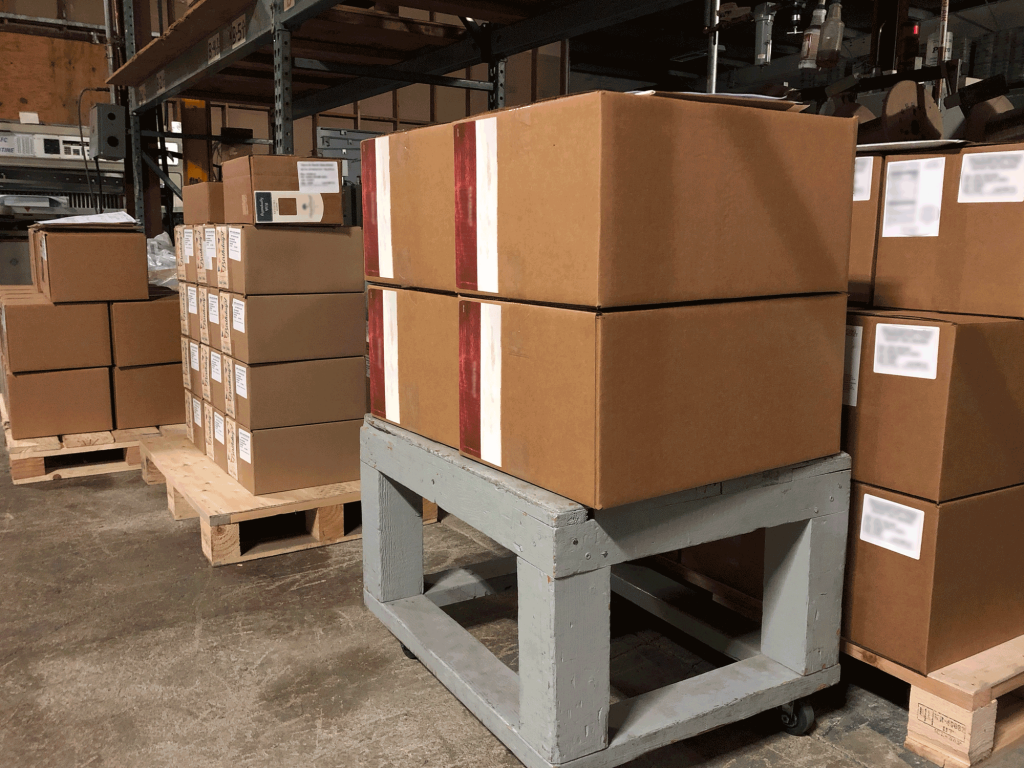